
CRB, a leading global provider of integrated project delivery solutions for food and beverage manufacturers, announced it has been chosen by Kikkoman Foods, Inc. to perform engineering, procurement and construction services (EPC) for its new soy sauce production facility in Jefferson, Wisconsin.
The 240,000-square-foot facility will produce Kikkoman's signature sauce and sauce-related seasonings, expanding the company's North American manufacturing footprint with a facility designed for automation and energy efficiency. On 100 acres in Jefferson, Kikkoman's newest brewing plant will draw on CRB's full spectrum of EPC services. CRB's project team will leverage the firm's deep experience in the food and beverage industry to meet Kikkoman's unique requirements, while delivering on its vision for the efficient and sustainable production of its iconic sauce and seasonings.
CRB's integrated project delivery model brings together cross-functional teams of experts who collaborate from the project's inception through to design and construction. This approach ensures all aspects of the project are aligned with Kikkoman's business objectives, delivering a facility that is optimized for performance and future scalability.
"Kikkoman is proud to partner with CRB for their industry leadership and expertise in food manufacturing to help bring our vision for the new, state-of-the-art Jefferson facility to life," said Dr. Ryohei Tsuji, Executive Corporate Officer, President and COO of Kikkoman Foods, Inc.
Groundbreaking at the site, held June 12, marks the project's first major milestone leading to its initial shipments of soy sauce, expected in the fall of 2026. The plant, Kikkoman's third North American site, will include advanced automation and control systems and sustainability features designed to reduce carbon emissions through energy-efficient equipment and design. Additionally, the high-capacity facility was designed to accommodate significant expansion should Kikkoman seek future additions.
"It is an honor to join with Kikkoman in delivering a facility that will advance Kikkoman's legacy as a provider of the soy sauce that has become mainstay for millions of consumers, and certainly a staple in my own kitchen," said CRB President and CEO Ryan Schroeder. "This project represents the best of both companies: Kikkoman's manufacturing innovation paired with CRB's proven track record for delivering state-of-the-art manufacturing projects, on schedule and on budget."
Write comment (0 Comments)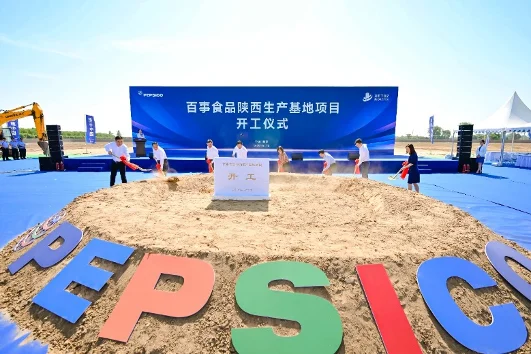
PepsiCo’s first food production base in Northwest China officially broke ground in Xi’an, Shaanxi, adding innovative vitality to the high-quality development of the Western region. The PepsiCo Food Shaanxi Production Base is PepsiCo’s fifth major investment in China in the past five years, with an estimated total investment of $180 million (RMB 1.3 billion). The base is built by the internationally advanced “net zero emission” standard and is expected to enter the trial operation stage in September 2025. The production capacity is expected to reach approximately 25,000 tonnes to meet the growing consumer demand in the seven provinces of Northwest China.
This time, PepsiCo will establish a new milestone in China in the Shaanxi Xi’an Economic Development Zone, and work closely with the local government to accelerate the efficient implementation of the project from site selection, project establishment, and contract signing to groundbreaking. This further demonstrates its long-term commitment to continue to deeply root in the Chinese market and achieve win-win results with regional partners. It is also a reflection of its determination to respond to the call for regional economic development and help promote the formation of a new pattern of Western development.
The PepsiCo Foods Shaanxi Production Base is the tenth food factory established by PepsiCo in China, with an initial investment of $80 million and a construction area of approximately 32,000 square meters. It is equipped with two new automated potato chip production lines, and supporting warehouses, storage cold storage, power facilities and wastewater treatment facilities. As a brand-new digital demonstration factory in the northwest region, the base will introduce advanced automated production, packaging and warehousing technologies, and is committed to making positive contributions to local industrial upgrading and talent development.
Write comment (0 Comments)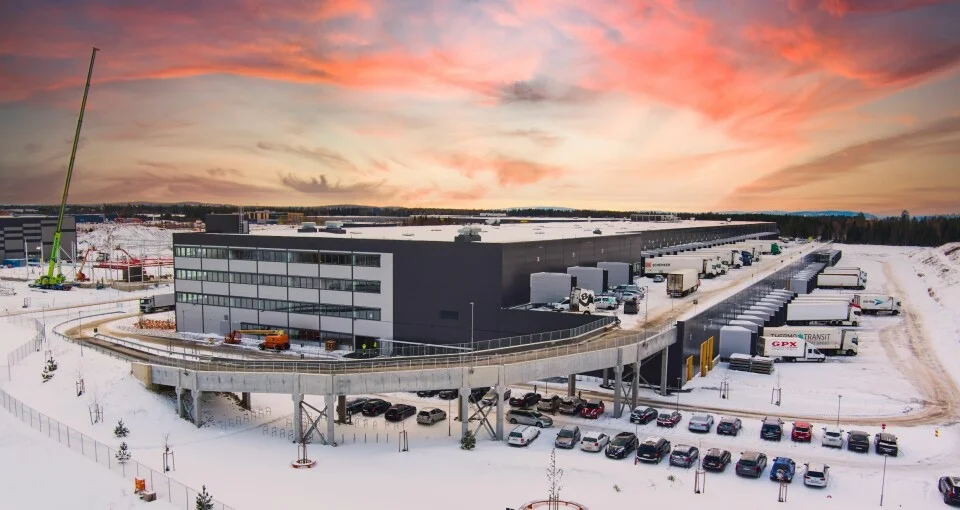
Slate Asset Management (Slate), a global alternative investment platform targeting real assets, announced that it has acquired the World Seafood Centre, a state-of-the-art, newly built seafood refrigeration and distribution facility, located in one of the most prominent and well-connected logistics hubs, Oslo Airport City, in Gardermoen, Norway, for approximately NOK 1.3 billion.
The acquisition further scales Slate’s portfolio of essential real estate assets in Europe and expands Slate’s real estate footprint in the Nordics.
The seafood industry is the second largest and growing export industry in Norway and benefits from strong demographic tailwinds that are driving high demand for seafood industrial space in the region. The World Seafood Centre is a 55,000 square-meter facility strategically located in the rapidly developing Gardermoen region within Oslo Airport City with immediate access to main transport networks to Europe and overseas markets in Asia and America. The property is let to some of the largest seafood tenants in the world under long lease terms indexed with CPI, which are expected to provide stable and resilient cash flows. The facility derives 100 per cent of its energy supply from green and renewable sources and is equipped with robotics and artificial intelligence technologies, which further contribute to its high levels of operating and energy efficiency.
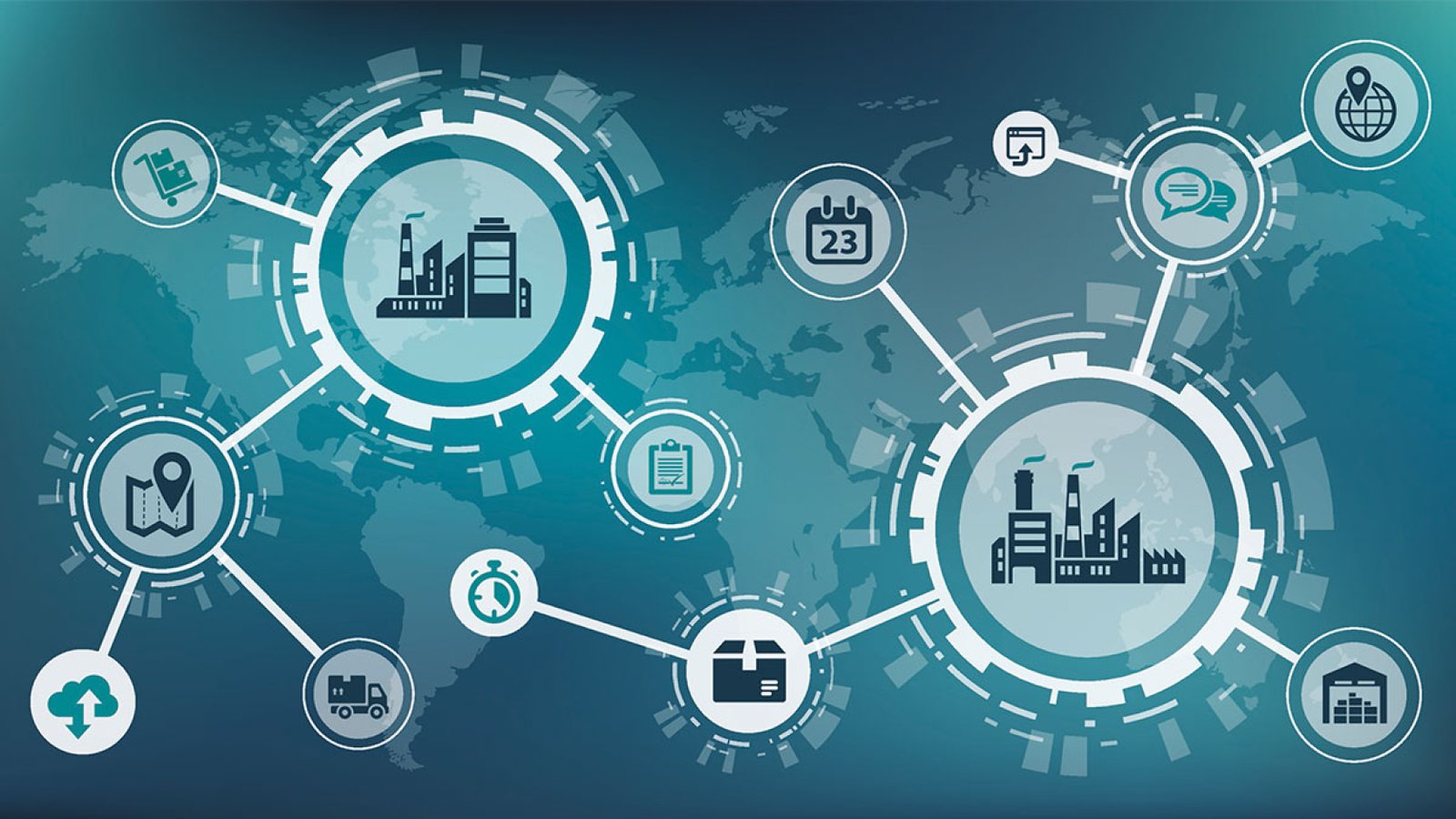
Campbell Soup Company announced plans as part of an ongoing effort to invest in and transform its supply chain to fuel business growth, improve return on invested capital, and enhance the overall effectiveness and efficiency of its manufacturing and distribution network.
These actions are another significant step in transforming Campbell’s supply chain into a competitive advantage. The company is investing in its best-in-class manufacturing sites, leveraging its network of leading co-manufacturing partners, and closing inefficient sites and shifting production to more modern and effective plants.
“To fuel growth and transform our manufacturing and distribution network, we must invest and further strengthen our supply chain,” said Dan Poland, Campbell’s Chief Supply Chain Officer. “By leveraging our best-in-class in-house capabilities combined with the expertise of trusted manufacturing partners, we will continue to make the highest quality products, with a more agile, flexible, and cost-effective manufacturing network. We continue to evaluate optimization opportunities across the network to build our supply chain of the future.”
Tualatin, Oregon Plant to Close
The Tualatin, Oregon plant, acquired in 2017 as part of Campbell’s purchase of Pacific Foods, produces Pacific’s organic soup, broth and plant-based beverages. The site consists of multiple leased buildings of approximately 250,000 square feet. The aging facility and inefficient nature of the site’s configuration can no longer support the increased consumer demand and continued growth of the business.
Campbell will close the facility in phases and expects to cease operations by July 2026, with the first phase to impact 120 of its 330 employees in August 2024. The company plans to move the plant’s soup and broth production to other thermal and aseptic plants in its network and shift plant-based beverage production to leading co-manufacturing partners.
Jeffersonville, Indiana Plant to Specialize in Late July
The company’s Jeffersonville, Indiana plant will specialize in Late July tortilla chips. Production of kettle potato chips will be moved to Campbell’s Charlotte and Hanover plants. The change will go into effect in July 2024 and will impact approximately 85 of the 230 employees at Jeffersonville. The plant will continue to produce regional snack brands.
In total, the closure of the Tualatin site and the changes to the Jeffersonville plant will impact 415 employees. The company will provide impacted employees with separation benefits and job placement support.
Poland said, “We recognize this is difficult news for our teams in Tualatin and Jeffersonville. Any action that impacts our people is made with careful deliberation, and we are committed to provide support and assistance during these changes.”
To enable the supply chain network of the future and unlock the growth of the business, the company is making capital investments of approximately $230 million through fiscal 2026 at newer, more agile facilities in its network, with approximately $80 million spent to date. These projects are expected to create approximately 210 new roles across the organization and will include new training and development programs for employees.
Write comment (0 Comments)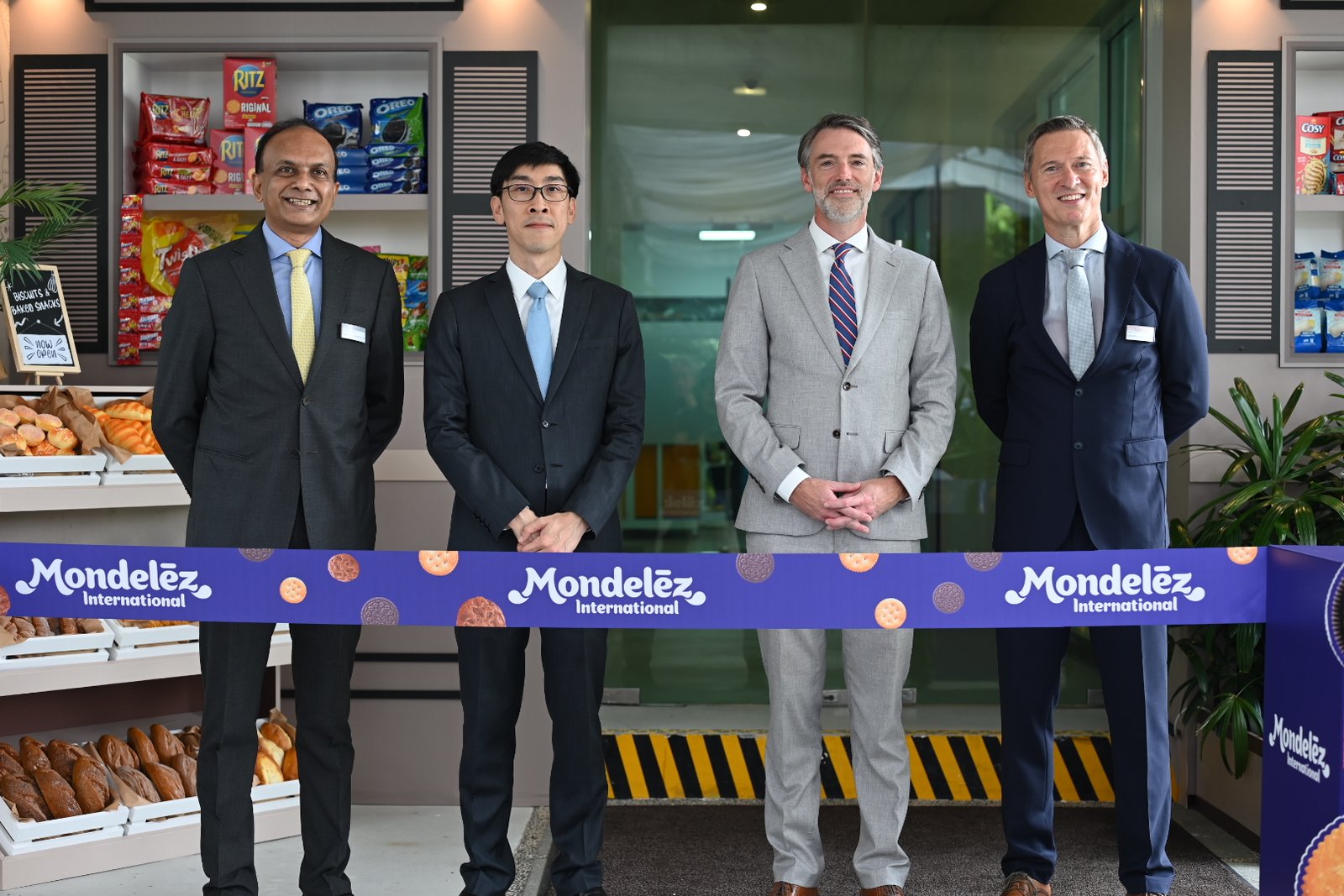
Mondelēz International, announced the inauguration of its Regional Biscuit and Baked Snacks Lab and Innovation Kitchen in Singapore, reaffirming its commitment to innovation and product development across Southeast Asia and Australia, New Zealand and Japan. This new facility was officially opened today by Mr Chan Ih-Ming, Executive Vice President, Singapore Economic Development Board.
The Lab and Innovation Kitchen will serve as a strategic Centre of Excellence and regional hub driving creative development and innovation in the biscuits and baked snacks category. Backed by more than $5 million USD investment, the facility expands on the capabilities of the company’s existing Singapore Technical Centre, established in 2006, followed by an expansion in 2018 to focus on innovation and product development in the gum and candy category.
"At Mondelēz International, we are dedicated to pushing the boundaries of food innovation and product development. Through collaborative efforts, we aim to create a dynamic space where creative ideas can flourish and contribute to the development of new innovative products for our consumers,” said Deepak Iyer, Executive Vice President & President AMEA, Mondelēz International. “This expansion further enhances the capabilities of our Singapore Technical Centre and reaffirms our commitment and contribution to the country, which serves as the headquarters for our Asia Pacific, Middle East and Africa business.”
With a focus on co-innovation, this expansion is designed to help accelerate MDLZ’s mission to create "the right snack, for the right moment, made the right way.” The establishment of the Biscuit and Baked Snacks Lab and Innovation Kitchen marks a significant step in MDLZ's commitment to mindful snacking, including developing products that encourage portion balance and mindful indulgence whilst exploring flavor innovation and different product formats.
Today, the Singapore Technical Centre houses expertise and technical capabilities in Product Development, Packaging, Process Technology Development, Consumer Science, Analytical Science, Ingredient Research, and Scientific and Regulatory Affairs. Through this expansion MDLZ aims to build on these skillsets, upskilling existing talent and evolving employee capabilities to drive deeper consumer-driven innovation and advance operational effectiveness.
Commenting on the inauguration of the Regional Biscuit and Baked Snacks Lab and Innovation Kitchen, Mr Chan said: “The expansion will capitalise on opportunities presented by the rising Asian middle class, and a growing appetite for premium and responsible snacking experiences. Singapore, which is at the heart of Southeast Asia and boasts a vibrant food ecosystem, presents an ideal location for such endeavours. We are proud to stand alongside Mondelēz International as they embark on this new and exciting journey to delight consumers with every bite!”
Write comment (0 Comments)